Chemical Resistant
Epoxy Novolac Coating
Highly Chemically Resistant Novolac Epoxy Floor
Coating and Novolac Epoxy Wall Coating
100% Solids - Zero VOC Chemical Resistant
Product #633
Novolac Epoxy Coating Description
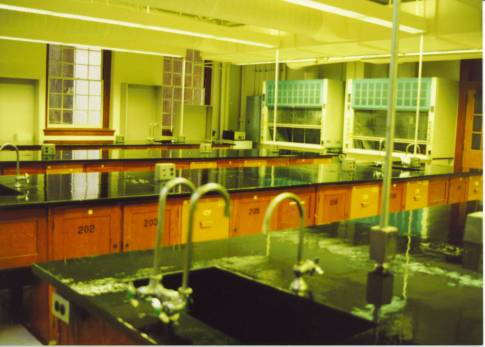
Product #633 Novolac Epoxy Chemical Resistant Epoxy Coating is a 100% solids epoxy Novolac
coating ideal for harsh chemical and solvent resistant applications.
Product #633
is used in secondary containment, solvent storage, pump pads, trenches,
and other high exposure areas.
Novolac Epoxy - Highly Chemical Resistant Epoxy - Product #633 is ideal for use as a protective
coating for concrete and steel in the extremely corrosive areas of
chemical plants and pulp mills secondary containment areas, water and
waste treatment, and gas and electric utilities. Product #633 is commonly used as a seal coat for
EPOXY MORTAR SYSTEMS where chemical resistant performance
is required.
NOVOLAC EPOXY #633
ADVANTAGES
- Exhibits excellent resistance to strong acids, alkalis, and most
industrial chemicals and solvents
- Can be applied in cool damp conditions
- Can be re-coated in 4 to 6 hours
- Can be applied in occupied facilities
- Forms a virtual moisture barrier
- Meets USDA standards
- 100% solids - 0.0 lbs VOC - meets even the most strict low VOC requirements
CONSIDERATIONS
- Concrete substrate to receive
Product #633 Novolac Epoxy must be free of dirt, waxes, curing agents, and
other foreign materials.
- Steel surfaces to receive Product #633 Novolac Epoxy must be free of grease and oils. Abrasive blast to
SSPC-SP5.
COMPOSITION
- 100% solids, modified amine adduct cured epoxy Novolac resin.
APPLICATION
SURFACE PREPARATION
Surface Preparation is the most critical portion to
any successful resinous system application. All substrates must be
properly prepared as outlined in
Epoxy
Surface Preparation Procedures.
Concrete to Receive Chemical Resistant Novolac Epoxy Coating #633
Surface must he clean and sound. Remove all dirt,
laitance, grease curing compounds and other foreign
matter by sandblasting, mechanical abrasion, or acid
etching. Remove water and dust from all surfaces with an
oil-free blast immediately prior to application.
Steel to Receive Chemical Resistant Novolac Epoxy
Coating #633
Immersion Service
Sandblast to near white metal - (SSPC10 / NACE2).
Non-Immersion Service
Sandblast to Commercial Blast (SSPC10 / NACE3)
For more information on surface
preparation please see the
Epoxy.com Surface Preparation Guide.
INSTALLATION of Chemically Resistant Novolac Epoxy Coating #633
Installation methods for
Product #633 will vary with application method. See
Coating Installation Guide for use in typical coating
applications.
Mixing
Stir both component with separately before mixing
together. Be sure not to cross contaminate the "A" into the "B" or
visa versa. Mix for 3 minutes using an Epoxy.com (drill) mixing paddle
or equal on a low speed drill.
If Anti-Skid Course or Anti-Skid Fine is to be used add 12-16 volume ounces per mixed gallon,
and mix until properly dispersed, typically 1-2 minutes.
When Used as a Coating
When Product #633 is applied over concrete or
wood, prime with Product #12
Chemical Resistant Epoxy
Primer and allow the Product #12 Primer to cure to tack free.
Priming is optional over gray metal blast steel.
Application of Product #633 can be done by
brush, roller, squeegee, or airless spray. Airless spray is best
done with higher end binary airless spray equipment.
For typical installations as a coating apply 2
coats of Product #633 Novolac Epoxy at a
rate of 160-200 square feet per gallon per coat. This yields
a wet film thickness of 8-10 mils thick per coat or 16 - 20 mils for the
two coats. Since this is a 100% solids Resin and
Hardener
system, there is no loss during drying, so the wet film thickness and
the dry film thickness for 2 coats will be identical (16-20 mils DFT).
If Anti-Skid Fine or Anti-Skid Course
epoxy anti-skid additive is used add plus or minus 12 volume ounces of Anti-Skid per mixed gallon
of Product #633. Never add more than 16 volume
ounces per gallon of Resin and Hardener mix.
PHYSICAL PROPERTIES
|
Color
|
See color chart below
|
Solids Content
|
100%
|
Gloss 60 F
|
100
|
Mix Ratio
|
2A to 1B by volume
|
Pot Life
|
20 minutes @ 75 F
|
VOC
|
0%
|
DRY TIME |
Foot Traffic
|
10-12 hours
|
Recoat - Minimum
|
4 - 12 hours (Depending on Temperature)
|
Recoat - Maximum
|
24-36 hours (Depending on Temperature)
|
Service
|
5 days
|
CHEMICAL RESISTANCE
|
REAGENT |
RATING |
Acetic Acid 20% |
R |
Acetic Acid 56% |
L - 24 hour |
Acetic Acid 84% |
L - 24 hour |
Acetic Acid (Glacial) |
L - Hourly Cleanup |
Acetone |
L - Hourly Cleanup |
Bleach |
R |
Citric Acid |
R |
Crude Oil |
R |
Diesel Fuel |
R |
Ethylene Glycol |
R |
Fatty Acids |
R |
Gasoline |
R |
Hydrochloric Acid-36% |
R |
Hydraulic Fluid
|
R
|
Lactic Acid |
R |
Methyl Ethyl Ketone |
L - Hourly Cleanup |
Nitric Acid - 10% |
R |
Perchloroethylene |
R |
Propylene Glycol Monomethyl Ether |
R |
Skydrol |
R |
Sodium Hydroxide - 50% |
R |
Sodium Hypochlorite 10% | R |
Sulfuric Acid-10% |
R |
Sulfuric Acid-50% |
R |
Sulfuric Acid-70% |
R |
Sulfuric Acid-98% |
R |
Toluene |
R |
Urine |
R |
Xylene |
R |
R-Recommended for continuous service L-Limited recommendation,
occasional spills.
PERFORMANCE PROPERTIES
|
Tensile Strength ASTM-D-638 |
10,400 p.s.i |
Adhesion to concrete ACI Committee 403 |
300 p.s.i - 100% concrete failure |
Hardness ASTM-D-2240 |
86 Shore D |
Abrasion Resistance ASTM-C-501 CS-17 Wheel |
30 mg lost |
Service Temperature MIL- D-3134F |
Up to 180-325 degrees F. Dry Heat |
Elongation |
2.5% |
Click
the picture of
color card below for a larger version of this picture of the color
chart.
Please
note:
The picture to the right is a photographic reproduction of the color
card for this product. The photo reproduction process and your monitor
and/or printer will change these colors. This chart is to give you an
idea of the colors available and not intended for critical color
selections.
Chemical Resistance Chart for Product
#633
|
Chemical |
Resistance
|
Acetone
| S-3
|
Acetic Acid 56%
| S-2
|
Acetic Acid 84%
| S-2
|
Acetic Acid (Glacial)
| S-3
|
Aluminum Chloride 30%
| +
|
Aluminum Nitrate 50%
| +
|
Aluminum Sulfate 50%
| +
|
Ammonium Hydroxide -30%
| +
|
Ammonium Sulfate 50%
| +
|
Ammonium Sulfide 50%
|
+
|
Barium Sulfate
| +
|
Barium Sulfide
| +
|
Beer
| +
|
Benzene
| S-2
|
Benzyl Alcohol
| +
|
Black Liquor
| +
|
Butyl Acetate
| +
|
Butyl Acetate (Normal)
| +
|
Brake Fluid
| +
|
Butanol (Normal)
| +
|
Calcium Chloride
| +
|
Calcium Hydroxide
| +
|
Carbon Tetrachloride
| +
|
Citric Acid -40%
|
S-1
|
Corn Oil
| +
|
Crude Oil - Sour
| +
|
Crude Oil -Sweet
| +
|
Cumene
| +
|
Cutting Oil
| +
|
Cyclohexeone
| +
|
Diacetone Alcohol
| +
|
Diesel Fuel
| +
|
Diethylene Glycol
| +
|
Distilled Water
| +
|
Ethanol
| +
|
Ethyl Acetate
| +
|
Ethyl Alcohol
| +
|
Ethylene Dichloide
|
S-1
|
Ethylene Glycol
| +
|
Ethyl 3-Ethoxypropionate
| +
|
Ethylene Oxide
| +
|
Ethlene Glycol Monopropyl Ether
| +
|
Freon
|
S-1
|
Fuel Oil
|
+
|
Gasoline (Unleaded)
| +
|
Gasoline (Premium Unleaded)
| +
|
Glucose
| +
|
Glycerine
| +
|
Glyoxal 40%
| +
|
Heptane
| +
|
Hexane
| +
|
Hexalene Glycol
| +
|
Hydraulic Fluid
| +
|
Hydrochloric Acid 10%
| +
|
Hydrochloric Acid 36%
| +
|
Hydrogen Peroxide -5%
| +
|
Hydrogen Peroxide 30%
| +
|
Iodine
| +
|
Isobutyl Alcohol
| +
|
Isopropyl Alcohol
| +
|
JP 4 Jet Fuel
| +
|
JP 5 Jet Fuel
| +
|
Kerosene
| +
|
Ketchup
| +
|
Lactic Acid 50%
| +
|
MAK
| +
|
MEK
| S-3
|
Methanol
| +
|
Methylene Chloride
|
NR
|
MIBK
| +
|
Mineral Spirits
| +
|
MTBE
| +
|
Naptha (VMP)
| +
|
Nitric Acid 10%
| +
|
Nitric Acid 30%
|
NR
|
Oxalic Acid
| +
|
Para Xylene
| +
|
Peanut Oil
| +
|
Perchloroethylene
| +
|
Phosphoric Acid 10%
| +
|
Phosphoric Acid 75%
| +
|
Phosphoric Acid 85%
| +
|
Power Staring Fluid
| +
|
Propylene Glycol Monomethyl Ether
| +
|
Propylene Glycol Monomethyl Ether Acetate
| +
|
Pseudocumene
| +
|
Skydrol 500B
| +
|
Sodium Hydroxide 50%
| +
|
Sodium Hydroxide 70%
| +
|
Sodium Hypochlorite 10%
| +
|
Sodium Nitrate 50%
| +
|
Sulfamic Acid
| +
|
Sulfuric Acid 10%
| +
|
Sodium Bisulfiate
|
S2
|
Sulfuric Acid 50%
| +
|
Sulfuric Acid 70%
| +
|
Sulfuric Acid 98%
| +
|
Toluene
| +
|
Tomato Juice
| +
|
Transmission Fluid
| +
|
1.1.1 Trichloroethane
| +
|
Urine
| +
|
Vinegar
| +
|
Vinyl Tolene
| +
|
White Liquor
| +
|
Xylene
| +
|
+ = Continuous Service (greater than 6 months)
S1 = Splash and Spill with Weekly Cleanup
S2 = Splash and Spill with 24 hour Cleanup
S3 = Splash and Spill with Hourly Cleanup
NR= Not Recommended
ND= No Data
|
Other customers who visited this page also visited:
You can estimate using the spreadsheet below or by using our
Coating Calculator.
